If the customer is not satisfied nothing else matters! Customers want the best possible product/service as soon as possible and at the lowest cost possible. Business that strive for customer satisfaction, are always looking for various means to delight the customers. Lean is one of those remarkable principles that help you know how to delight customers by delivering the right products/services, at the lowest cost possible within the shortest time.
What is Lean?
In today’s fast paced world, speed and agility of process is a critical factor that enables quick delivery to customers. Lean is a business approach based on the fundamental goal of eliminating waste and maximizing flow. A Lean Organization is one that fully understands, communicates, implements, and sustains lean concepts seamlessly throughout all operational and functional areas. The lean process is one in which all members of a company are involved and obsessed about eliminating waste.
The 5 Principles of Lean
- Define Value – From the customer perspective capture the voice of customer for delivering delightful experience
- Value Stream Mapping – Diagnose the pulse of the process through data based detailed analysis from the prospective of customer
- Continuous Flow – Ensuring a seam less progress of value adding activities for delivering a symphony of service or product delivery
- Pull Production – Ensuring flexibility and responsiveness to ever changing need of customers
- Strive for Perfection – Proactively be on your stride to create Next mark performance
Why do companies need Lean?
Lean as a methodology for a problem solving helps companies ?
- Diagnose the Value Stream
- Eliminate Waste from process resulting in to
- Faster and responsive delivery
- Create opportunities for top line enhancement
- Making offering cost competitive
- Involve everyone and create a culture of passion for perfection
Combining Lean with Six Sigma can be especially powerful. Six Sigma focuses on defect reduction whereas Lean and lean manufacturing principles focus on speed of delivery. Used together, these two methodologies help companies improve their processes critical to customer satisfaction.
Where is it applicable?
The Lean methodology/Lean manufacturing principles is equally effective in solving problems related to both transactional and manufacturing environments.
Lean and TPE
In the context of Total Performance Excellence (TPE), Lean principles/tools and lean manufacturing services are most effectively employed when your intent is to make key, subordinate and enabling processes function as waste-free as possible. It is easiest for companies to undertake Lean after they have solidified their strategic direction, put process architecture into place and aligned the business around that architecture.
BMGI’s approach for problem solving through Lean roadmap
BMGI deploys Lean principles/ lean manufacturing services using the Lean Roadmap. The improvements that need to be brought for moving to desired state of value stream are Kaizen (change for the good) events. BMGI’s lean consulting experts use its proprietary SCORETM Methodology for demystifying the deployment of Kaizen in the Lean journey.
BMGI’s lean consulting experts use its proprietary SCORETM Methodology for demystifying the deployment of Kaizen in the Lean journey.
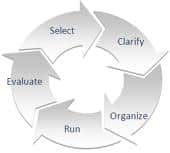
BMGI deploys expert lean consultants through a series of consulting and training interventions. BMGI also offers Open Enrolment and In-house courses on Lean. To learn how Lean interventions can solve your problems or to know more about our Open Enrolment and In-house programs, contact BMGI.