How many times you have faced problems due to customers rejecting your product/service because of defects or faulty specifications? Would you not have wished your processes to run at 100% perfection? 100% perfection might seem to be too ideal to achieve in the real world but 99.9996% is possible.
What is Six Sigma?
The term “Six Sigma” refers to the capability of processes to produce output within specifications with high degree of precision. In particular, processes that operate with six sigma quality produce at defect levels below 3.4 defects per million opportunities (DPMO). Six Sigma ’ inherent goal is to improve all processes to that level of quality or better.
Six Sigma is a set of tools used for making business decisions originally developed by Motorola to systematically improve processes by eliminating defects. A defect is defined as nonconformity of a product or service to its specifications. While the particulars of the methodology were originally formulated by Bill Smith at Motorola in 1986, Six Sigma is heavily inspired by six preceding decades of quality improvement methodologies such as quality control, TQM, and Zero Defects.
Why do Companies Need it?
Companies use Six Sigma to reduce variation in products and processes- but the net effect of any Six Sigma intervention is what people are really looking for- fewer defects, shorter cycle times, increased capacity and throughput, lower costs, higher revenues and reduced capital expenditures. Organizations deploying Six Sigma over a long term see the culture of the organization getting transformed to a more systematic problem solving approach and more importantly, people making data driven decisions.
When Six Sigma is deployed systematically and pervasively- with the right support and leadership force – it helps in reducing the Cost of Poor Quality (COPQ) to produce large amounts of cash for short-term profitability or for long-term investments. Recently many companies deploy the TRIZ methodology for problem solving and product design as part of a Six sigma approach.
In addition to Motorola, companies that adopted Six Sigma methodologies early on and continue to practice it today include Honeywell International (previously known as Allied Signal) and General Electric (introduced by Jack Welch).
If you have not adopted Six Sigma yet, what are you waiting for!
The Six Sigma Method – DMAIC
Define – | Define a problem or improvement opportunity |
Measure – | Measure process performance |
Analyze – | Analyze the process to determine the root causes of poor performance; determine whether the process can be improved or should be redesigned |
Improve – | Improve the process by attacking root causes |
Control – | Control the improved process to hold the gains |
Some practitioners add an ‘R’ for “Recognize“ in front of Define and an ‘R ’ for “Realize & #8221; after Control. You first have to ‘Recognize ’ the problem before defining it and have to control it after implementing a solution to ‘Realize’ its financial benefits
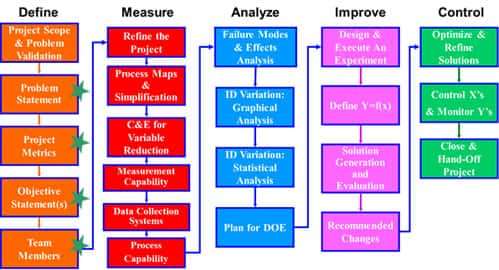
While Six Sigma follows the DMAIC methodology at the project level, it follows a well-established deployment methodology at the business level. Companies like GE and DuPont have paved the way for making Six Sigma deployable through large networks of Champions, Black Belts, Green Belts, Yellow Belts and Process Owners.
BMGI’s Approach for Problem Solving through Six Sigma
For many years, BMGI’s Six Sigma experts has helped clients address their largest business challenges. Whether the goal is to reduce costs, achieve long-term growth, improve overall business performance or maximize revenues, BMGI has been there to help its clients build results.
Working closely with clients every at each step, our consultants and expert trainers follow a four-step business improvement process that begins with goal setting and planning, follows.

through to program development and deployment, and ends with goal realization and handover for internal management.
Our business improvement process is demonstrated below. This process is designed to deliver tangible results in the shortest possible timeframe as well as to “in-source” capability within the organization to be able to take over, drive and expand the initiative independently without BMGI support.
One size fits all! Or does it? That is why BMGI customizes it’s framework to suit organizations’ vision and objectives for problem solving through Six Sigma initiative, their current state of readiness and their culture. Through various interventions as shown below, BMGI is able to work with client organizations and deliver results.
- Building a shared vision of the Six Sigma journey. This is achieved through executive awareness sessions, one-on-one meetings with the senior management team and planning sessions
- Building the necessary infrastructure in terms of policies and procedures required for long term sustenance of the Six Sigma initiative
- Establishing the framework for identification and prioritization of the right interventions that are aligned with the organization’s business goals and strategy
- Executing these interventions through internal resources of the organization or through master consultants from BMGI. Where required, BMGI would create the requisite capability within the organization on problem solving through Six Sigma tools
- Strong project and program management to ensure the initiative is progressing as planned
While building and executing this roadmap, BMGI’s ability to integrate with the client organization at an operating level has helped in managing the resistance to change and keep the momentum of the initiative going.
BMGI’s Consulting and Training Program
At BMGI, we understand that learning happens best when the participants can relate to the subject being taught. To provide the best learning experience, BMGI’s Six Sigma experts has customized its training material for the manufacturing as well as service industry verticals. Our structured training materials are designed on whole-brain approach and on lines of the Adult Learning Model of LEKDACH. This ensures that the concepts are better understood and retained by the participants.
Six Sigma Master Black Belt Experts on Hire
Many organizations want to have access to expert resources whenever they face critical operational problems which cannot be solved from internal resources. To facilitate this, BMGI’s Six Sigma experts offer unique expert services where BMGI’s experienced Master Black Belt consultants assume the roles of a Black Belt and lead projects with support from the process experts in the organization to solve the critical issues. This practice has gained popularity and many organizations have achieved significant benefits from our expert services. To know how BMGI’s Master Black Belt consultants can help you solve your problems, Contact BMGI.